Resources - Blog
Summer residents: Sophie Zajicek
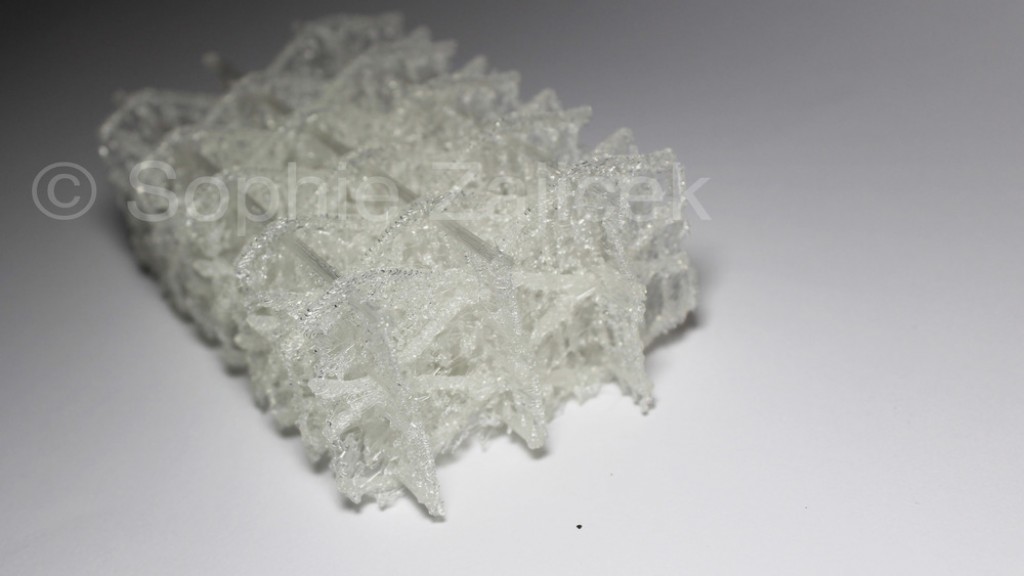
Over the summer of 2015 RSA Great Recovery hosted a number of Summer Design Residents at Fab Lab London. These young designers were all developing circular economy projects, and were seeking out access to machinery and circular economy expertise to help them make their ideas a reality.
Sophie Zajicek, a weave designer and RCA graduate, is investigating the potential to create 3D printed ‘woven’ structures.
GR: Hi Sophie, tell us a bit about your project
Whilst at the RCA I worked with Oluwaseyi Sosanya who was developing a 3D weaving machine. It’s very similar in concept to a 3D printer, and I really wanted to further develop my ideas for printing ‘woven’ structures. My work is going in a really exciting direction at the moment – using Fab Lab London as my base and source of all 3D printing knowledge. I’ve been developing 3D printed materials that are based on woven structures, with the circular economy model ever present in every stage of the design process.
Developing textiles for the circular economy is achievable through the use of a 3D printer. A traditional weaving loom creates waste at the start and finish of each warp and a selvedge along the edges of the fabric that is then discarded. I can see potential in 3D printing to reduce or wastage.
Using the 3D printing facilities I am developing material samples that aid my research into creating shock absorbing textiles solely from one component. Cutting out any excess waste and additional materials usually required for spacer/ shockproof fabric. Using a 3D printer to create textiles enables me to transform traditional weave structures from the x and y axis into the x,y and z. It frees one from the constraints of a loom and adds a third dimension to the fabric.
GR: How did having access to Fab Lab and The Great Recovery support you in developing your ideas?
SZ: Through The Great Recovery and Fab Lab I have been able to develop my circular project design theory. I have relied heavily on the expertise of the Fab Lab team throughout my design development as I went into this project with no knowledge of 3D printing. During my time at Fab Lab I have slowly begun to understand the limitations of the machines, the software, the materials and therefore begun to realise the holes in my initial project aims.
The Great Recovery have given me a deeper understanding of the circular economy and the problems faced by manufacturers and designers when trying to tackle this challenge. However, I have only scratched the surface and am keen to push my project further.
GR: What challenges have you come up against as you’ve tried to design for circularity?
SZ: Sourcing and interpreting data has been a challenge. And because 3D printing is a new field for me getting to grips with the various software programmes has been a huge learning curve and has used up much more of my time than I anticipated. Whilst the technology is really versatile I’ve also found it hard to achieve the desired outcome using the materials I have access to in the Lab. A combination of these challenges has slowed down the development of this project.
I am in the process of testing a new software program, Gravity Sketch,which has been developed to give designers a more intuitive method of designing 3D forms. It is this transition between Gravity Sketch software into Rhino and then into product I have been experimenting with. This process has been a huge learning curve for me, as I find Rhino totally unintuitive to navigate, which is where Gravity Sketch comes in. On top of this designing process I’ve had to learn how to use various 3D printer software and learn that patience has a whole other meaning when dealing with all of them together on one computer, in a short space of time!
GR: What role do you think makerspaces, like Fab Lab, have in helping people design circular products and systems?
SZ: Fab Lab is the perfect platform to help designers initiate projects when facilities and space are incredibly hard to come by. Having expert advice on tap has been a big advantage and being able to access many different machines in one area, using a variety of different materials, is a great way to encourage immediate creativity and design development of circular products.
Find out more about Sophie’s work here